- FMA
- The Fabricator
- FABTECH
- Canadian Metalworking
EM Dynamics invests in fibre laser to speed, expand capabilities
For over 40 years, the Toronto-based company has been fabricating and machining products for clients around the world
- Updated April 23, 2020
- April 24, 2020
- Article
- Fabricating
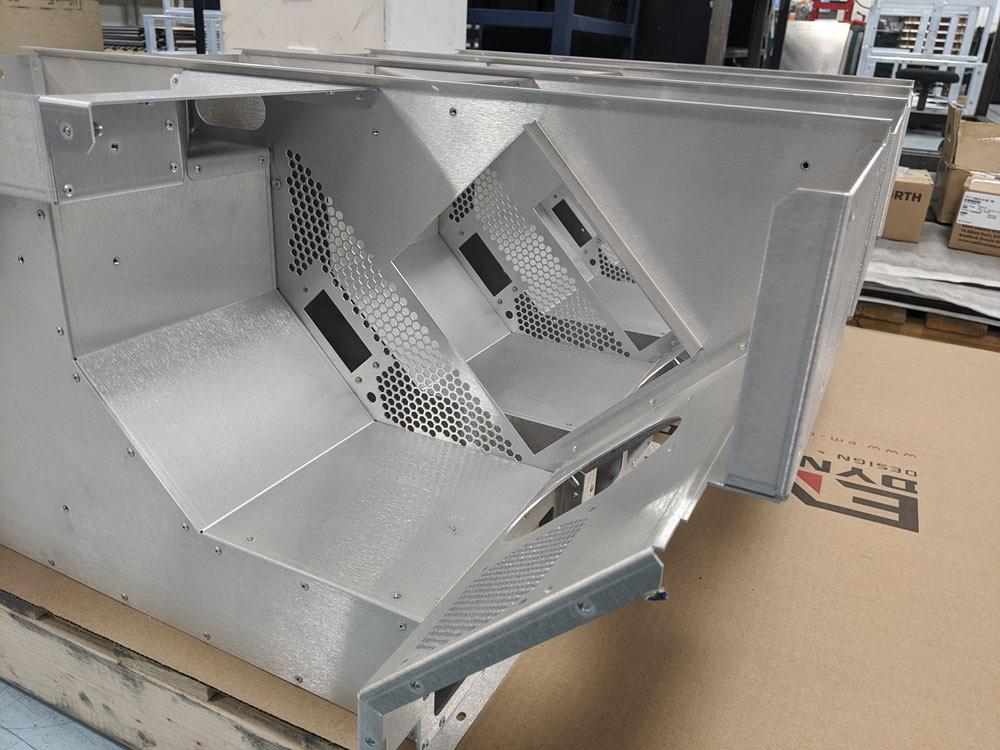
This part, made from 14-ga. 5052 aluminum, is designed to go on the frame of an HDR projector. In this instance, the shop used the fly cutting feature on the laser to cut out exhaustholes. This method decreased cut time by 400 per cent for this part.
For over 40 years, Toronto-based EM Dynamics has been fabricating and machining products for clients around the world. Operations at its two buildings, which encompass 130,000 sq. ft., include design, manufacturing, and integration expertise for vertically integrated contract manufacturing and assembly.
Business growth has required numerous investments in new machinery. Most recently that included an 8-kW fibre laser.
“Our business was rapidly expanding, and we needed a laser that could keep up with and stay ahead of the curve of production,” said Dave Sidhu, president of EM Dynamics. “The number of orders were growing beyond the limits of our capacity and we were longing for controls on the cost of production. There were also potential orders that we were unable to fulfil because our machine was too small.”
EMD’s previous machine, a CO2 laser, was not only too small (with cutting capacity limited to a maximum of 4 ft. by 4ft.), it was also unable to cut the material and thicknesses that customers were requiring – everything from cold-rolled steel to stainless steel, aluminum, copper, and brass. They were also spending a lot of time and money on legacy punching machines that required expensive dies to be purchased and stocked. To bring in new clientele while still meeting customer needs, production requirements changed. EMD needed a machine that could load larger sheets of material and cut a variety of materials at much faster speeds.
“Even if we had met most of those requirements with our older machine, we would still have a lot more jobs headed to our finishing department to clean burrs off edges and vertices,” said Sidhu. “We required a machine with the cut quality that would allow us to eliminate many cleanup operations. In the long run, we needed a machine with the tools and performance to lower our cost of production.”
Cutting Capabilities
EMD’s search for a reliable and capable fibre laser cutting machine from a reputable brand led it to investigate four suppliers. The final decision was to go with Mazak’s Optiplex 3015 Fiber III 8-kW machine.
“I was blown away by the machine’s cut quality and variety of machine controls,” said Sidhu. “The benefits that those two features could play in our company’s future were glaringly obvious to me. For instance, you can program simple parts on-the-fly, change cut conditions quickly, and even edit programs for future cuts while the machine is running. In terms of nesting, we currently use Radan software.”
One of the newer technologies that improves cut quality on this machine is Mazak’s multi-control torch, which adjusts the beam diameter and nozzle to suit both the material and thickness so that cutting parameters are optimized. Maximum sheet size on the bed is 1,525 mm by 3,050 mm (5 by 10 ft.).
While performance and capability are essential, they were not enough for Sidhu and EMD.
“The main reason we believe in Mazak was their competency and support,” Sidhu further explained. “Erin Chasse, Mazak’s regional manager, was very keen on understanding our needs, our process, and our future ambitions. He gave us the machine blueprint, machine options, and services that we needed to set ourselves apart from our competition and thrive in the future.”
Results
Since installation of the fibre laser, EMD has experienced immediate results.
“It is evident that the machine’s ability and promise were no exaggeration. The benefits are increases in four major categories for a metal fabricator: cut speed, cut quality, material cut range, and sheet size,” said Sidhu.
“The machine saves us money through its speed and quality. It saves us manpower through its customized options and controls. Most importantly, it speeds up our time to market.”
As a job shop, EMD works with various customers in an assortment of industries that require rapid prototyping, new product introductions, and manufacturing.
“For example, the medical and military markets are primarily in the business of saving lives. Our new laser cutting machine gives us the ability to provide customers the comfort of receiving their parts within the sensitive time frame that they desire to support their critical industry.”
The materials the shop is cutting have broadened also.
“On the new laser we routinely cut steel, stainless steel, and aluminum,” said Sidhu. “Less regularly, we cut brass, copper, tin, and other coated materials. We have also run tests on tungsten. When we had our older laser, we only cut steel, stainless steel, and aluminum.”
Ultimately, the laser also affects downstream operations also.
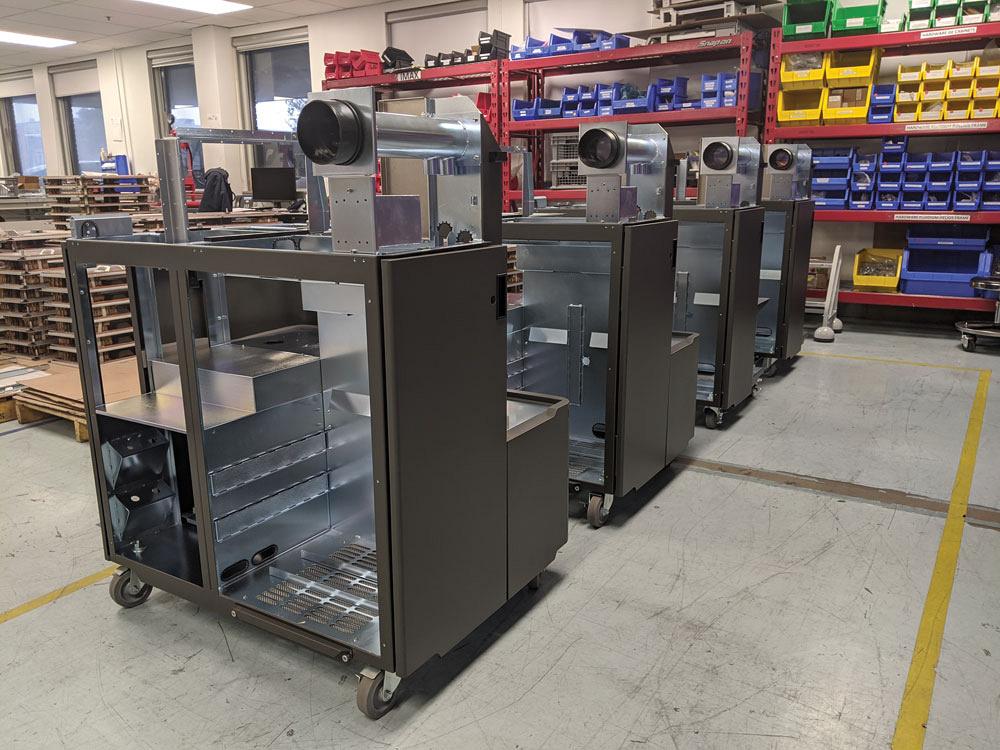
This 14-ga. cold-rolled steel assembly was built for a medical device company. The shop used clean cutting with nitrogen to provide burr- and oxide-free edges. This method decreased secondary finishing operations drastically.
“Our forming centres have less downtime than they did in the past,” said Sidhu. “We have since added new press brakes and have been able to match their capacity. The quality and speed of the laser in comparison to what we had in the past shows that if you invest in resources upstream, it can increase flow downstream exponentially – and that’s what we have done here.”
Philanthropy at Home and Abroad
While EMD serves customers all around the world, it also serves both its local community in the GTA and in Sidhu’s ancestral home in Punjab, India.
“We have many disparities in our state of Punjab,” said Sidhu. “Our home village of Chakar became devoid of unity, faith, and resources. For my family, it was critical to do what we could to help out and pave a path for the youth. Family members and friends that shared a similar goal helped implement a new wave of belief and support there. A few initiatives included a complete revamping of the sewer system structure, clean water irrigation, planting tens of thousands of trees at a time, new community/senior centres and repaving of major roads.”
Sports were also a passion for the Sidhus so they wanted to pass it on to communities both locally and internationally to give children opportunities where resources often are hard to come by. This led EMD to create the Sher-E-Punjab Sports Academy in 2006. This academy gives children free memberships to participate in sporting culture, specifically boxing and soccer. “Ever since its fruition, the academy has nurtured several athletes that have gone on to dominate every stage of competition, from regional to international.”
EM Dynamics also supports many charities, sports clubs, and humanitarian efforts in Ontario. More information can be found on the company website at https://em-dynamics.ca/community-investment/.
EMD team members try to demonstrate leadership capabilities both on and off the shop floor. Not only do they aim to provide exceptional work as a company, they also set a standard for how to give back to the communities that matter most.
EM Dynamics, www.em-dynamics.ca
Mazak Optonics Corp., www.mazakoptonics.com
subscribe now
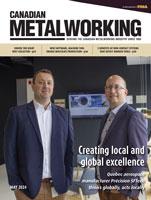
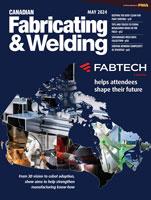
Keep up to date with the latest news, events, and technology for all things metal from our pair of monthly magazines written specifically for Canadian manufacturers!
Start Your Free Subscription- Industry Events
Automate 2024
- May 6 - 9, 2024
- Chicago, IL
ANCA Open House
- May 7 - 8, 2024
- Wixom, MI
17th annual Joint Open House
- May 8 - 9, 2024
- Oakville and Mississauga, ON Canada
MME Saskatoon
- May 28, 2024
- Saskatoon, SK Canada
CME's Health & Safety Symposium for Manufacturers
- May 29, 2024
- Mississauga, ON Canada